maintenance & repairs.
We have a modern workshop equipped with all the necessary tooling to assemble, test, and service fluid systems. From our facility in Enschede (NL), we are fully capable of performing maintenance and repairs on your system.
Our standard maintenance protocol includes a visual inspection, a functional check, and the replacement of wear-and-tear parts as needed. All work is documented in an inspection report, provided for a fixed-price inspection fee.
If the system’s condition requires it, we will create a repair offer that includes the replacement of any faulty key components.
Please contact us using the maintenance & repair form to obtain an offer, or feel free to reach out to us directly.
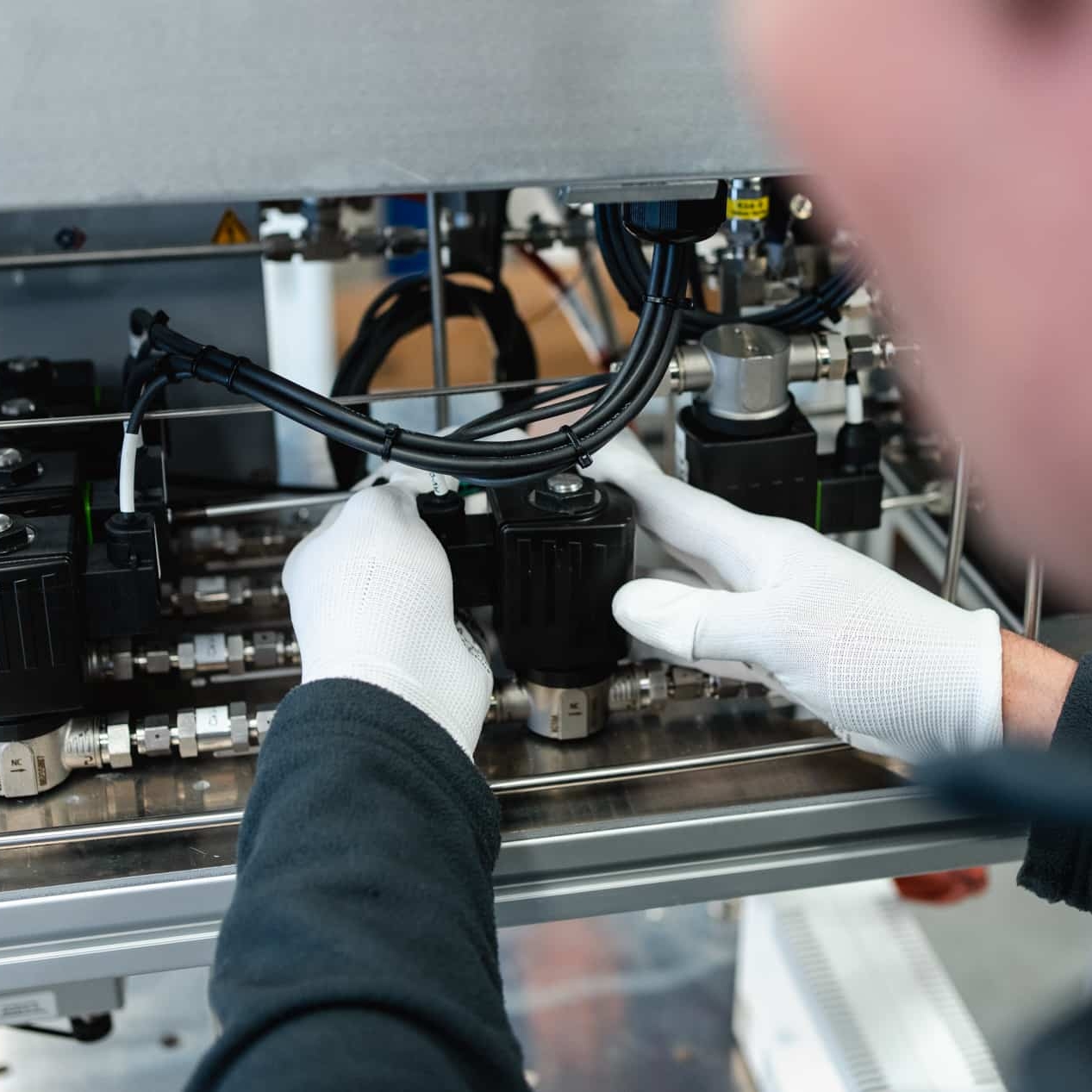
retrofits.
Over time, some customers may need to operate their systems outside of the original design envelope due to changing use cases. In certain situations, exchanging a pump can result in a system that meets the new performance requirements. However, this must be assessed on a case-by-case basis, as changing a key component like a pump can significantly impact various elements of the system’s design.
Potential impacts include changes to pressure drop, pressure rating, and the suitability of existing instruments for the new duty. Additionally, an update to the technical documentation, including the risk management file, is required to complete the retrofit. Depending on the starting point, a new system might be the better option.
Please contact us to request a retrofit engineering study and we will advise you on the best suitable option for your situation.
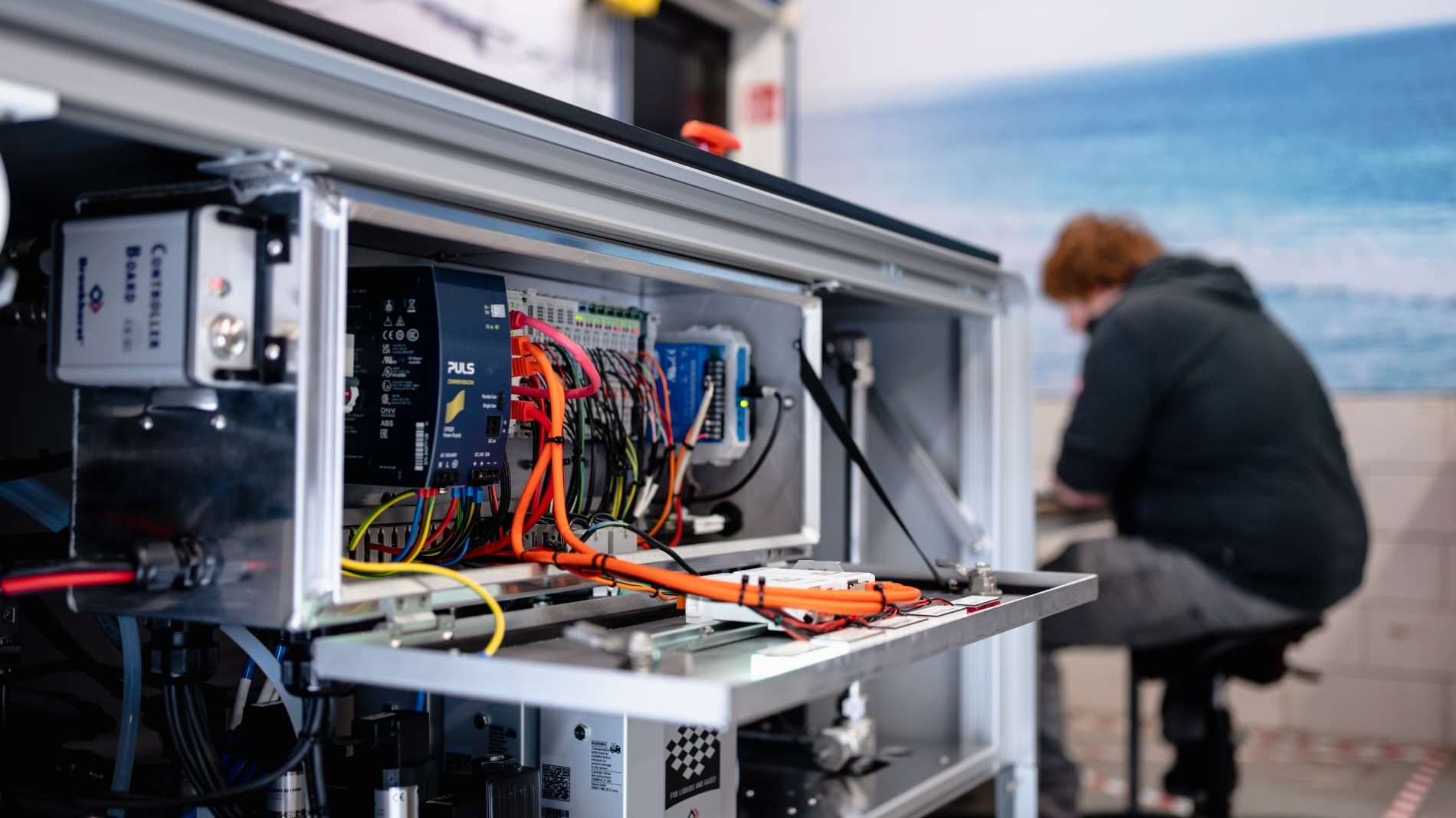
instrument calibrations.
Process instruments like flow meters, flow controllers, and pressure sensors experience wear from the conditions of the process in which they are installed. Temperature, electronic component tolerance shift, contamination build up over time, plus other factors will all contribute to affecting the accuracy of an instrument.
To keep the instruments inside of your system in peak working condition and to guarantee its continued accuracy, periodic calibrations and/or service is often required.
Because the nature of each application is different (conditions, running time, etc.) a calibration can last from two years to three months. Our systems do not have specified due dates for calibration, but we often see that most high-end user adhere to an annual calibration cycle for optimal results and usage.
For a calibration, the system needs to be returned to our facility in Enschede in order to unmount the instruments to gain proper access for the actual calibration work.
Most customers request the standard ISO 9001 certification. For some users, calibration in an ISO 17025 accredited laboratory is required. We work with a number of accredited external laboratory to also provide this service. Please note that the latter has a substantial longer lead-time, leading to a longer down-time of your system.
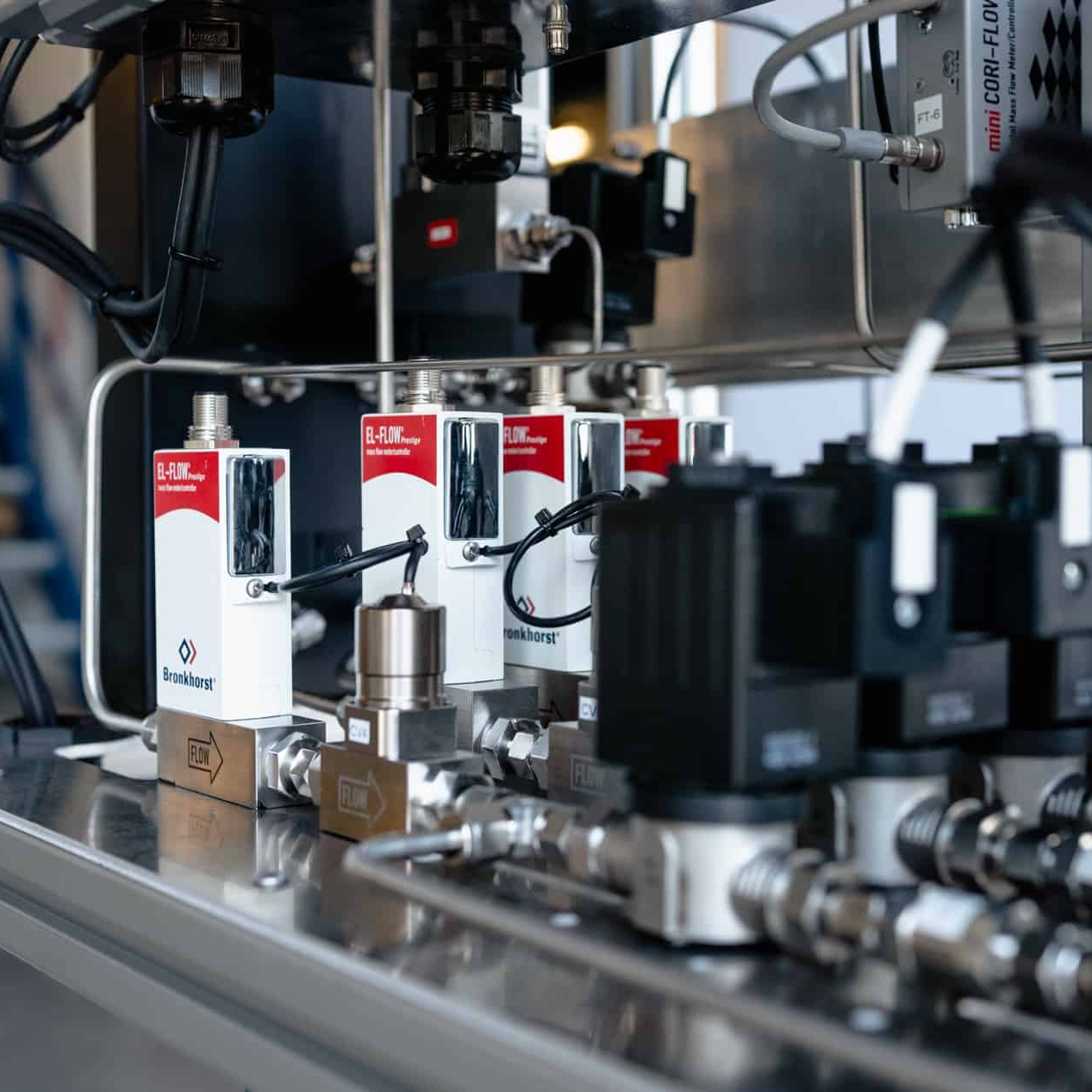
training & support.
We offer training courses to inform you on all the ins- and outs regarding our systems and how to use them. The training is typically aimed at users, researchers, operators and technicians and helps you to become more productive with our equipment. If needed, a particular focus to a topic of interest can be made.
Although all systems are shipped with a complete manual, most customer do buy an initial online training to get started. This is also recommended for optimal usage of our systems. Moreover, users that do not use the system regularly or have gone through team changes, can benefit of a refreshment training.
For customers that have very specific needs or are experiencing issues after warranty, we also offer half day sessions to provide support and troubleshooting online.
Contact us using the form if you want to book a training or a support session.
Serviceform training
Serviceform support
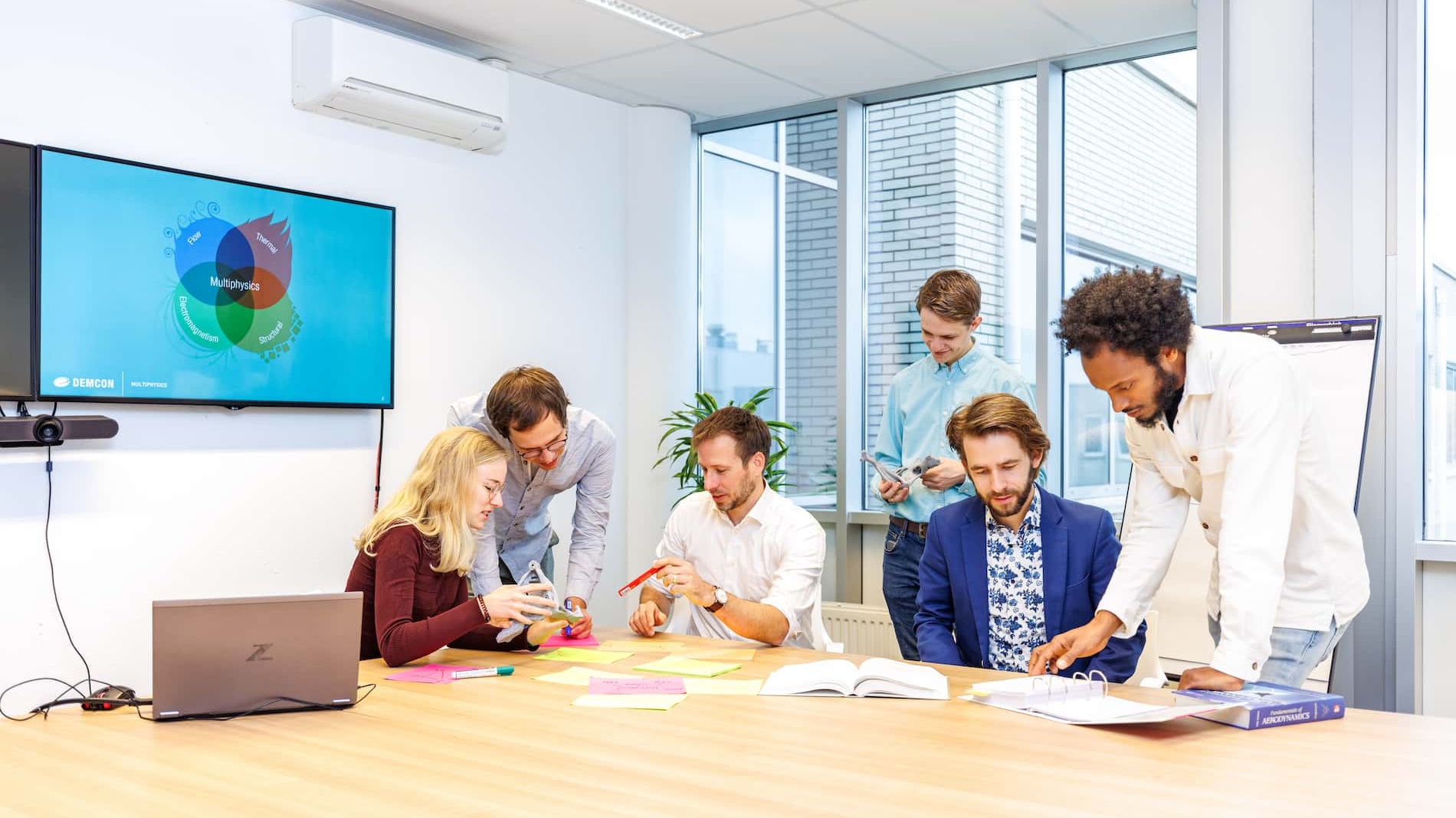
spare parts.
We supply our systems with a recommended spare parts list, which includes the key components needed to keep your system up and running. Users can choose to keep spare parts in stock for preventive maintenance or source specific parts after an unexpected failure.
Spare parts are delivered either directly from our stock or sourced from one of our trusted suppliers. Ordering through us ensures that you receive the exact part needed for your system, guaranteeing proper integration and functionality.
If you have any questions about delivery times and pricing of spare parts, please contact us using the form below or reach out to us directly.
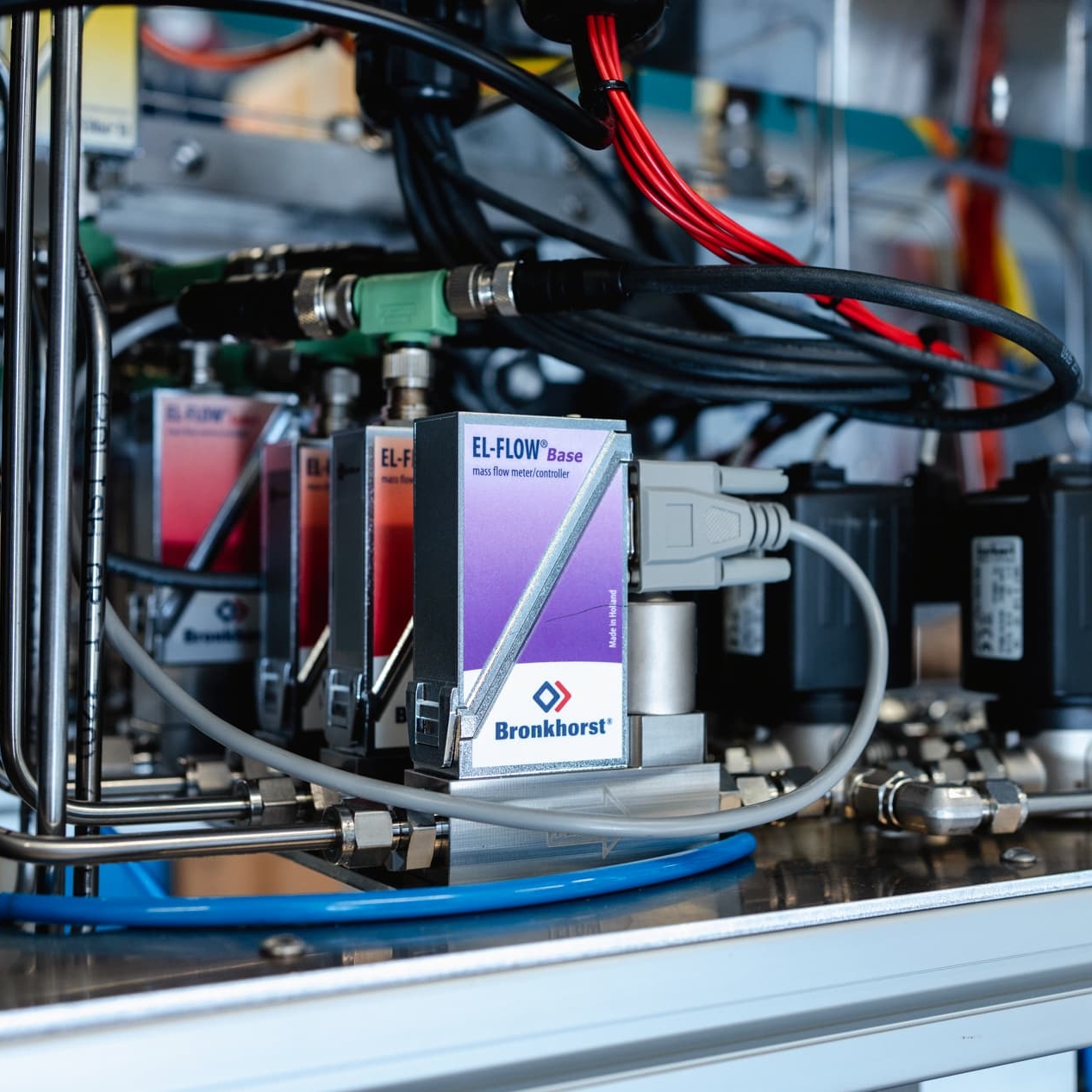
software upgrades.
FCP to FCP upgrades:
Systems operating on our Flow Control Platform (FCP) software can be upgraded to the latest version without any hardware issues or losing existing user programs. This upgrade is included in the FCP license. The latest version can be downloaded from our website at the software section.
Some customers prefer to outsource the installation to us. We offer a customized support session in which we will install the new FCP software remotely for you and make sure that the software is ready to use.
Legacy “OSMO” software:
From the company’s inception up to 2022, most of our systems have been supplied with our “OSMO” inspector software. Medio 2022 a next generation software suite called Flow Control Platform (FCP) was successfully released and is now used as the default software for all new systems. Starting July 2024 the support for the former “OSMO” software has ended. Therefore, we cannot provide any free software updates, technical assistance and fixes for this software anymore. Your system will still work but we advise most user to upgrade to our new FCP platform.
Upgrades from “OSMO” to “FCP”:
An upgrade to FCP will provide you with the opportunity to receive future updates and support. Moreover, you will benefit from a wealth of modern features that will increase the efficiency of your work.
Software upgrades from “OSMO” to “FCP” are always done in our facility in Enschede and cannot be performed remotely. All electric hardware like pumps and instruments need to be re-connected softwarewise to the platform. Legacy hardware or exotic communication protocols can cause hick-ups during this process that are best resolved in our factory by our specialist. After installation, the original flow sheets will need to be configured as well. This process is completed with a comprehensive functional test of the system in our facility.
Contact our service manager if you need more information about an upgrade.
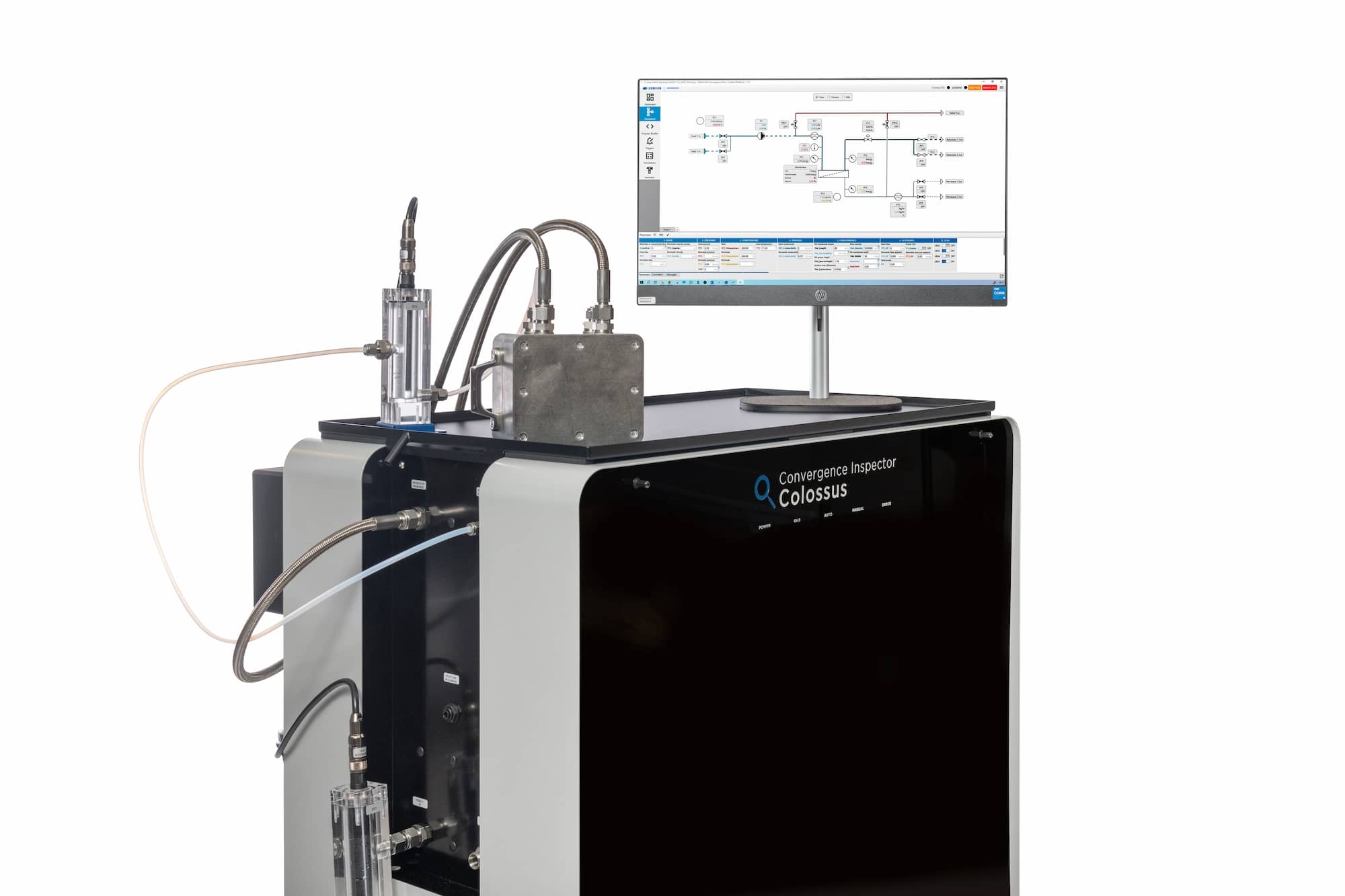